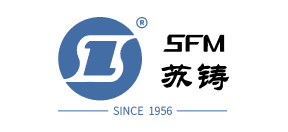
Flask moulding lines for green sand, sand plants, pouring units
Learn more
Flask moulding lines for green sand, sand plants, pouring units
Learn more
Flaskless molding lines for green sand, sand plants
Learn more
No-bake moulding equipment, reclamation plants for mixtures
Learn more
Low pressure die casting machines, gravity casting machines, tooling
Learn more
High pressure die casting machines, tooling
Learn more
Core shooter machines, tooling
Learn more
Induction furnaces for melting, holding and casting
Learn more
Spherodizing and graphitising modifiers, NiMg alloys
Learn more
Grinding cells
Learn more
Equipment for carburization, quenching (salt/oil)
Learn more
Chaplets and vents
Learn more
Pneumatic hammers and hydraulic wedge spreaders
Learn more
Exotermic riser sleeves
Learn more
Industrial manipulators
Learn more
Shotblasting machines
Learn more
Shotblasting machines
Learn more
Equipment for steelmaking workshops
Learn more