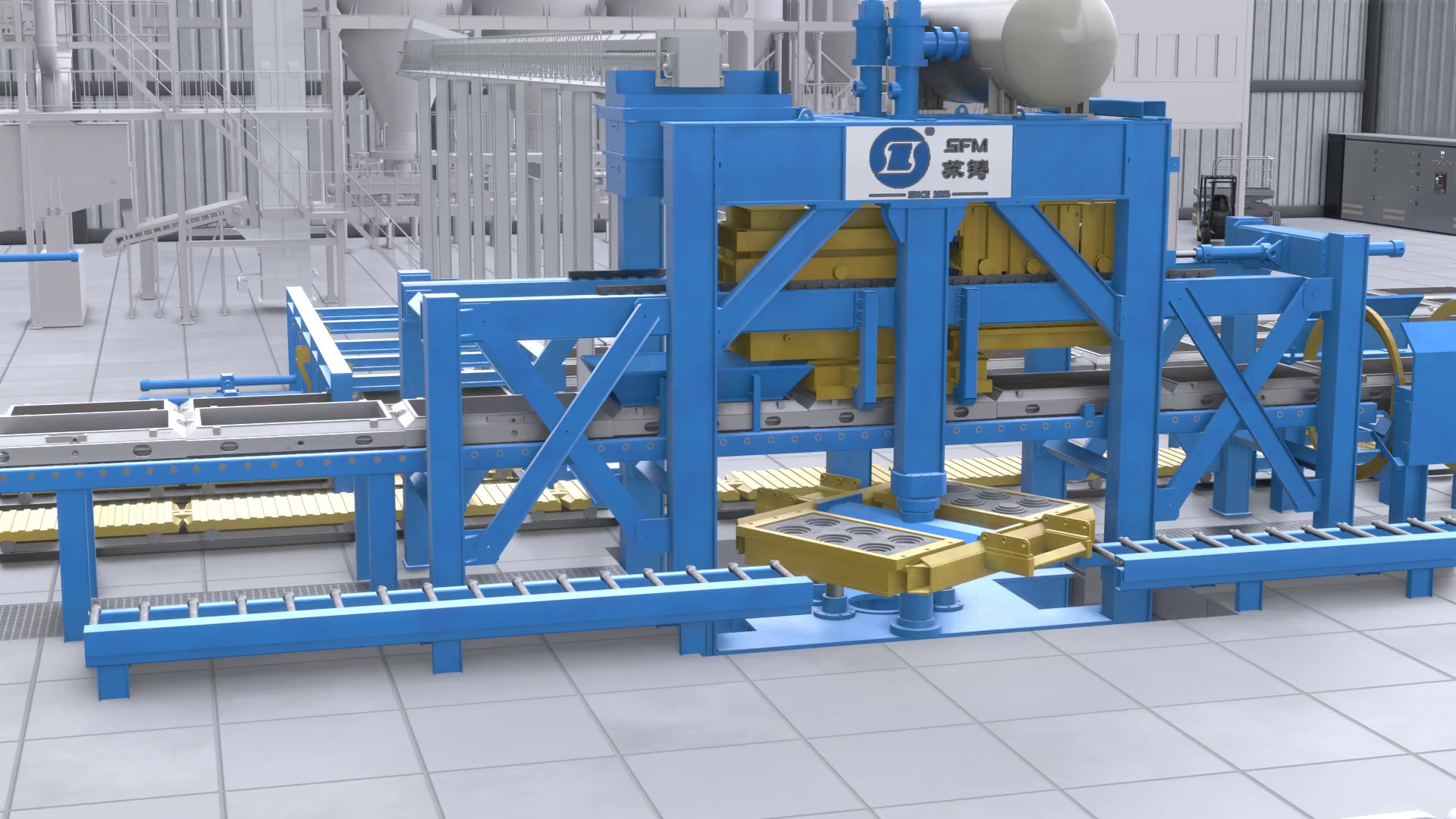
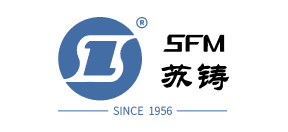
SFM
Flask moulding lines for green sand, sand plants, pouring units
The company SUZHOU FOUNDRY MACHINERY (SFM), founded in 1956, manufactures molding lines and sand plants for enterprises working on green sand technology, the first automatic line was produced in 1981.
With experience in the integrated implementation of more than 200 projects, SFM manufactures:
- Automatic molding lines with a capacity of up to 240 complete molds per hour;
- Sand plants with a capacity from 30 to 300 tons per hour;
- Unheated tilting type automatic pouring machines.
Automatic molding lines with a capacity of up to 240 complete molds per hour
The main technical features of SFM molding equipment:
1. There are 3 basic mold compaction methods: HP, HP+ A; DHP +A;
a. top pressing using a multi-plunger head (HP series of molding machines);
b. air pulse pre-compaction + top pressing using a multi-plunger head
(HP + A series of molding machines);
c. air pulse pre-compaction + top pressing with a multi-plunger head + lower pressing with a moving frame
(DHP +A series of molding machines).
Depending on the customer’s requirements, there are customized solutions regarding the compaction method — combinations of HP+A+D, HP+A-S, DHP+A-S, HP +A-S pro, HP-S and others.
The variability of the choice of the compaction method allows the customer to choose the optimal one, which allows to obtain a high-quality mold.
At that time, the maximum size of the flasks on ever producing molding lines is 2500 ×1500 × 600/500 mm.
SFM supplies complete solutions based on an automatic molding line + a complete Sand plant + an Unheated tilting pouring machine + a Ground liquid metal transfer system.
Advanced automatic molding lines are equipped with a green sand compaction control system, a moisture control system, automatic pattern change stations, automatic core setting devices, automatic devices for drilling sprue and ventilation holes, etc.
The main customers of molding and pouring equipment are enterprises from the automotive, tractor construction sectors, manufacturers of hydraulic equipment and spare parts for railways.
Technical features of SFM equipment:
- Multi-plunger head with a separate hydraulic cylinder for each plunger;
- The system of combined in-mold cooling (in flasks + multilevel in metal jackets).
Advantages for customers of using a combined in-mold cooling system:
- Saving space for the cooling system. This feature is due to the placement of the cooling lines in metal jackets on several levels;
- Saving on a fleet of flasks. 1 metal jacket accommodates 2 molds. The cost of 3 jackets (with 6 molds) = the cost of 1 set of flasks;
- Rigid casted flasks and trolleys made of grey cast iron;
- The possibility of using 2 sizes of flasks in the line;
- Flasks moving systems based on hydraulics with proportional control and electromechanical pushers in the areas of core setting and automatic pouring;
- Milling of the sprue and drilling of vent holes according to the coordinates set by the operator at any point of the mold.
Molding line 1 flask dimensions 1500 × 1400 × 380/300 mm, Capacity — 80 molds per hour;
Molding line 2 flask dimensions 1300 × 1200 × 350/270 mm, Capacity — 80 molds per hour.
Molding line flask dimensions 1200 × 800 × 200/350 mm, Capacity — 150 molds per hour.
Molding line flask dimensions 2000 × 1100 × 450/400 mm, Capacity — 40 molds per hour.
Molding line flask dimensions 800 × 700 × 250/200 mm, Capacity — 160 molds per hour.
Green Sand Plants with a capacity from 30 to 300 tons per hour
SFM company equips automatic molding lines with green sand plants for regeneration and preparation of fresh molding sand with a capacity from 30 to 300 tons per hour, including:
- belt and plate conveyors;
- bucket elevators;
- polygonal screens;
- sand coolers;
- sand mixers;
- pneumo conveying systems;
- green sand humidity control systems;
- green sand control systems (compaction, compression strength).
Unheated tilting type automatic pouring machines
Automatic unheated tilting pouring machines of the PU series are based on the «predictive» control algorithm developed by SFM. The stable mechanical design, precise four-point weighing technology, advanced vision technology for metal flow control and software provide the customer with a reliable and safe solution for pouring molds in fully automatic operation.
Advantages of PU Series Pouring machines:
- Three-axis positioning technology
All ladle tilting operations: up and down, forward and backward — are performed under servo control to ensure that the ladle is poured around a virtual fixed tilt point that can be adapted to different casting heights.
- Technology for controlling the casting process
The machine vision camera provides real-time feedback on the metal level in the sprue cup; the weighing sensor provides real-time feedback on the casting weight; the temperature sensor monitors real-time changes in the casting temperature.
- Synchronous casting technology
The continuous operation of the molding line during pouring is ensured by the synchronous operation of the servo drive of the filling machine and the hydraulic pusher of the line.
- Pouring control software
The SAPS2020 control software (SFM auto pouring system) is capable of implementing any separate manual operation and automatic operation of the pouring machine, as well as customizing and registering all data related to mold pouring.
Technical features of PU Series Pouring Machines:
- Three independent axis traveling (A, X, Y), each axis is driven by a servo;
- Tilting design with two-way drive;
- The machine is equipped with a weighting sensor;
- The machine is equipped with an optical mold filling sensor — online control of metal level in sprue cup;
- The machine is equipped with a late stream inoculation device;
- Full recording of the casting process;
- Fully automatic control of the casting process with a high degree of repeatability;
- Compatible with ladles of different shapes;
- Mold pouring is provided synchronously with the movement of flasks on the line;
- The machine is equipped with a metal temperature sensor.