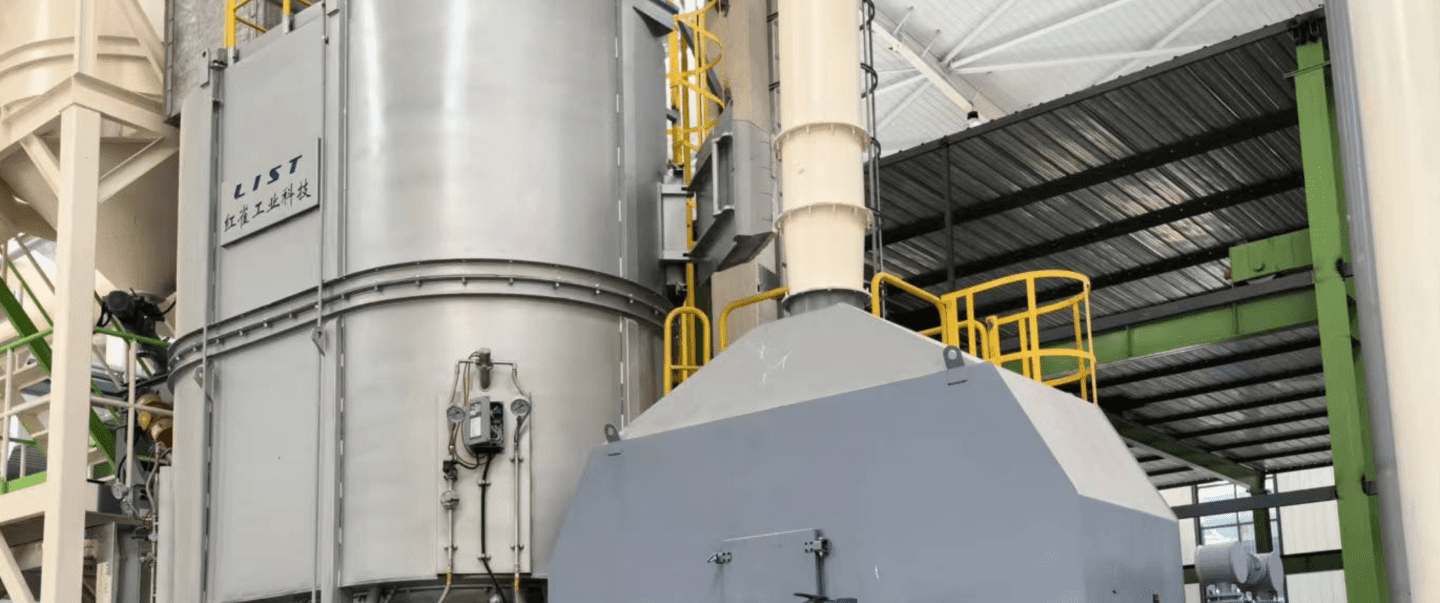
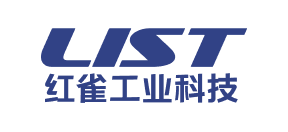
LIST
No-bake moulding equipment, reclamation plants for mixtures
Shanghai Linnet Industrial Science&Technology Co., Ltd (LIST) is a No Bake equipment design and manufacturing company that provides comprehensive professional production solutions, intelligent energy-saving equipment for No Bake process, sand reclamation equipment, sand transportation system, dust removal equipment and technical services for foundry companies. The company has passed the ISO9001:2015 quality management system certification.
The company was founded in 2012 in Shanghai, China. With highly qualified personnel and existing production capacity, the company is developing dynamically. In order to meet the rapidly growing demand for orders, the company invested in and built a modern production base of 122,000 square meters and a 10,000 square meter factory in Liuhe, Taichang in 2013.
Modern technological equipment and highly qualified workforce guarantee productivity and quality. For many years, LIST has been providing high quality service to its customers.
LIST not only has a strong design team, but also foundry expert resources, which can provide comprehensive solutions for modern foundries, including foundry planning and design, production process simulation, production efficiency analysis and key equipment.
Among the company’s more than 120 employees, a quarter are foundry engineers, ensuring strong design and development capabilities.
The company’s products and services include the design and manufacture of equipment for the No Bake process, including:
Continuous mixers from 1 till 100 t/h
- Single arm mixer
- Double arm mixer
- Three-arm mixer
Mobile mixers 15-100 t/h
The mixer is based on a mobile platform. The lifting conveying arm, sand mixing arm and sand outlet height can be adjusted. The conveyor arm has a built-in drive structure, which has better safety and stability.
Special mixers 2-6 t/h
The mixers are suitable for core production and small-scale production of small shapes. The mixer comes with a sand hopper and liquid component tanks that are easy to operate.
Automatic system for moulding of No Bake sand mixtures
Shake out grids
Robust design, high rigidity and durability. High-strength, structural steel, due to which the machine base has good impact resistance. Productivity 10-100 t/h. Carrying capacity of one section 10-60 tons.
- Model SOG-2ES
- Model SOG-EV
- Model SCM-G
- Model SCM-8G
Sand reclamation systems
- Lump crusher 10-30 t/h
The original design of the excitation mechanism, high efficiency and low energy consumption. The pneumatic design of the mixture discharge door effectively reduces the operator’s work intensity, and the design of the sieve reduces the amount of impurities in the sand.
- Mechanical reclamation 5-25 t/h
Applicable process: furan, alphaset, pep-set, liquid glass.
- Cooler/classifier 5-30 t/h
Cooling of sand in a fluidized bed. Mixture temperature at the inlet ≤ 300°C. Mixture temperature at the outlet ≤ 35°C.
- Vertical cooler 5- 20 t/h
Vertical static heat exchanger. Inlet sand temperature: ≤120°C. Outlet sand temperature: ≤30°C.
- Thermal reclamation plant 0,5-10 t/h
Gas: natural gas, liquefied petroleum gas, coke oven gas.
Process used: Cold box, Hot box, Pep-set, alkaline phenolic resins, clay sand.
- Pneumatic transport system
Propulsor APMC/S
Low-wear design for sand feeding can effectively improve the efficiency of sand feeding. Special design of inlet and outlet ensures faster sand feeding process into the pipeline.
Technical specifications: capacity 5-80t/h.
Tank capacity: 150L, 300L, 500L, 1000L, 1500L, 20000L.
Transported materials: quartz sand and other dry granular materials.